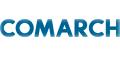
Produkcja w poszukiwaniu wydajności
- Szczegóły
- Kategoria: Artykuły
Dzięki funkcjonalności tego systemu szybko można uzyskać informacje o stopniu wykonania produkcji, podejmować na bieżąco decyzje i reagować na nieprawidłowości pojawiające się w czasie produkcji. Pozyskane dane pozwalają na analizę kluczowych wskaźników efektywności i uzyskanie prawdziwego obrazu wykorzystania zdolności produkcyjnych.
Podstawową przeszkodą w implementacji systemów MES w przedsiębiorstwach jest jednak długi czas wdrożenia oraz wysokie koszty inwestycji, które często są barierą niemożliwą do przekroczenia przez wiele spółek. Ponieważ jednak wolny rynek nie znosi próżni, pojawiło się rozwiązanie, które jest realną alternatywą dla kosztownych MES-ów. System Shop Floor Control stanowi uzupełnienie i rozszerzenie funkcjonalności ERP zapewniając precyzyjny pomiar wydajności pracowników i maszyn na linii produkcyjnej. Składa się ona z kilku modułów dedykowanych pod konkretny obszar produkcyjny (Kontrolę Jakości, Utrzymanie Ruchu, Raportowanie Produkcji, Rejestrację Czasu Pracy) - wszystkie moduły są dostępne na urządzeniach mobilnych.
Pomiar wydajności ludzi i sprzętu
Celem wprowadzenia rozwiązania Shop Floor Control jest poprawa efektywności produkcji poprzez szczegółową kontrolę procesów zachodzących na hali produkcyjnej. Zbieranie danych odbywa się na dwa sposoby. Pierwszy polega na automatycznym gromadzeniu informacji bezpośrednio z maszyn, takich jak ilość wyprodukowanych przedmiotów w danej jednostce czasu, informacje o zakończeniu danej partii, czy nieprawidłowościach i problemach technicznych. Drugim sposobem jest zbieranie danych przez pracowników za pomocą mobilnych ekranów dotykowych.
Każdy pracownik ma dostępny panel dotykowy z oprogramowaniem SFC które pozwala na ewidencjonowanie realizowanych czynności. Pracownik rejestruje postępy pracy przy powierzonych mu czynnościach. W trakcie i po ich wykonaniu wpisuje dane, co do wykonanej pracy, czyli np. ilości produktów, które udało się wytworzyć, ilości błędów, itp. Wprowadzenie danych może odbywać się przy pomocy kodów kresowych celem minimalizacji pomyłek.
Mobilna rejestracja na hali produkcyjnej
Wykorzystanie wersji mobilnej systemu SFC zapewnia szereg korzyści, począwszy od oszczędności czasu, po eliminację błędów wynikających z ręcznego wprowadzania danych z arkuszy papierowych. Jednym z głównych atutów oferowanych przez urządzenia mobilne jest możliwość wprowadzania danych bezpośrednio na linii produkcyjnej. Pracownik wyposażony w terminal, smartfon, czy tablet ze specjalną aplikacją może w czasie rzeczywistym raportować o postępach produkcji. Takie podejście do raportowania pozwala na efektywne planowanie produkcji uwzględniając wszelkie perturbacje, które mogą wystąpić podczas procesu wytwórczego.
Pracownik dysponujący urządzeniem przenośnym może wysłać sygnał do działu utrzymania ruchu o ewentualnych awariach czy usterkach maszyn, ograniczając stratę czasu (w standardowy sposób zobowiązany jest do wpisania awarii w kartę pracy lub przewodnik produkcyjny). Pracownicy utrzymania ruchu posiadający urządzenia mobilne np. smartfon wyposażony w system „Shop Floor Control - Utrzymanie Ruchu” mogą zawsze podejrzeć parametry maszyny, jakie należy wprowadzić podczas jej ustawiania w systemie. Informacje na temat parametrów są powiązane z odpowiednim zleceniem, co eliminuje ryzyko wystąpienia pomyłki.
Kolejną bardzo korzystną kwestią jest wykorzystanie urządzeń mobilnych przez działy kontroli jakości. Pracownik posiadający tablet z aplikacją „SFC - kontrola” może przeprowadzić walidację produktów w czasie rzeczywistym. W szybki sposób wypełnia wcześniej przygotowaną „check listę” i upublicznia ją odpowiednim osobom (np. działu handlowego). Dodatkowo system pozwala na załączanie zdjęć produktów, które posiadają defekt - ograniczamy wówczas czas jaki zazwyczaj był potrzebny na robienie zdjęć , wypełnianie papierowych „check list”, a następnie tworzenie raportu. Obecnie, takie operacje wykonuje się przy pomocy tabletu i właściwej aplikacji mobilnej.
Proste wyliczenie współczynnika OEE
System Shop Floor Control obsługuje zarówno pojedynczych pracowników, jak i brygady, czyli zespoły osób pracujących w jednym gnieździe produkcyjnym. Aplikacja umożliwia rejestrację ewentualnej awarii maszyny automatycznie informując o niej służby utrzymania ruchu. Pozwala to na szybką reakcję i naprawę, bądź wymianę wadliwego urządzenia, zachowując przy tym płynność produkcji. Dzięki pobranym w ten sposób danym, powstają raporty określające efektywność i sprawność pracy zarówno poszczególnych maszyn i urządzeń, jak i samych pracowników. Co więcej, dzięki temu istnieje możliwość przeprowadzenia dokładnego obliczenia współczynnika OEE.
OEE, czyli całkowita efektywność sprzętu, jest międzynarodowym wskaźnikiem określającym wydajność maszyn na produkcji. Mając dostęp do danych określających poziom wykorzystania poszczególnych urządzeń oraz pracowników, możliwe jest prowadzenie jeszcze dokładniejszych analiz wymaganych do optymalizacji procesu produkcji.
Alternatywa dla systemów MES
Aplikacja powstała w efekcie konsultacji z przedstawicielami firm produkcyjnych, które mają obawy związane z długotrwałą i kosztowną inwestycją w system MES. ASFC zapewniając precyzyjną informację o pracy maszyn i ludzi, realizuje część zadań rozbudowanego MES-a i pozwala na bieżąco optymalizować produkcję. Ponadto, dzięki rejestracji bieżącej produkcji w czasie rzeczywistym, system Shop Floor skutecznie wspomaga planowanie produkcji w systemach typu APS.
SFC może być alternatywą wobec kosztownych i czasochłonnych we wdrożeniu systemów typu MES. Wprowadzenie oprogramowania zajmuje jeden do dwóch miesięcy. Samo użytkowanie systemu jest niezwykle proste i intuicyjne – w żadnej mierze nie spowoduje perturbacji w pracy na produkcji. Co więcej, tworzenie zaawansowanych raportów również nie jest zadaniem skomplikowanym.
Autor: Piotr Rojek
Źródło: www.dsr.com.pl